Принятие решений на основе
балансовой теплотехнологической схемы (БТТС)
Перед тем, как начинать проработку каких-либо энергосберегающих мероприятий, нужно убедиться в наличии необходимой информации по стоящему вопросу. В нашем случае информацией являются технологические схемы производства, материальные и тепловые балансы агрегатов или узлов (хотя бы наиболее существенных), режимные характеристики потоков (температура и давление).
1. Формирование данных.
Эти данные формируются на основе:
- снятия показаний с узлов учёта и других приборов;
- аналитических определений составов потоков;
- расчёта удельных тепловых эффектов процессов, протекающих внутри агрегата или укрупнённого узла (теплоты химических реакций, теплоты парообразования и т.п.);
- приблизительной оценки того, что померить сложно (например, потери тепла в окружающую среду).
В качестве примера рассмотрим формирование исходных данных для печи риформинга производств на основе технологий оксосинтеза.
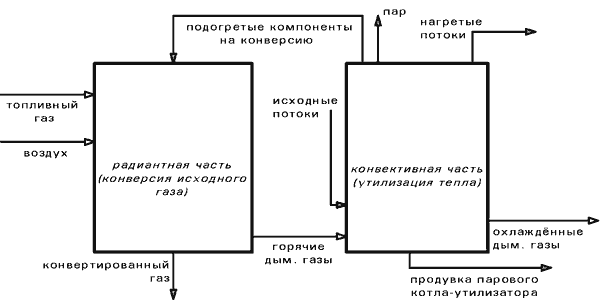
Для составления баланса данного агрегата необходимо иметь следующие данные:
- расходы топливного газа, пара с котла-утилизатора, исходных компонентов на входе в агрегат (кроме расхода питательной воды);
- давления топливного газа перед агрегатом, пара в котле-утилизаторе и в коллекторе после печи, исходных и промежуточных потоков на конверсию, конвертированного газа;
- температуры всех входящих, выходящих и промежуточных потоков (если пар насыщенный, то достаточно давления);
- составы топливного газа, исходных компонентов на конверсию, конвертированного газа, иных нагреваемых компонентов, горячих и охлаждённых дымовых газов (при качественном сгорании достаточно содержания кислорода), питательной и продувочной воды (солесодержание или общую щёлочность).
Эти данные служат для расчёта:
- расходов конвертированного газа, питательной и продувочной воды, горячих и охлаждённых дымовых газов;
- полных тепловых потоков (в единицу времени) на входе и выходе из агрегата и между его частями;
- ключевых технико-экономических показателей агрегата и его частей (энергетического КПД, удельного расхода топливного газа на единицу исходного или конвертированного, процента продувки котла-утилизатора и т.п.)
2. Представление данных.
Балансовые и технико-экономические показатели определяются в целом по агрегату и/или по каждой его части (в данном случае их можно разделить). Расчёт и формирование базы данных (для разных режимов, составов исходных продуктов или иных условий) удобно вести, например, в офисном приложении типа Excel.
Из вышеприведённых показателей для формирования картины энергопотребления необходимы следующие сведения: энергетическая эффективность работы агрегата (его частей) и ценность всех исходящих, промежуточных и выходящих потоков. Первая группа данных отражается в технико-экономических показателях составленного баланса (КПД и т.п.) и показывает качество работы агрегата и его соответствие паспортным показателям, а при их отсутствии аналогичным или подобным агрегатам, т.е. является характеристикой качества эксплуатации оборудования или энергетической характеристикой процесса. Вторая группа данных должна отразить эффективность выбранного метода использования исходных и промежуточных потоков и ценность выходящих потоков, как вторичных энергоресурсов (ВЭР), т.е. эксергетическую характеристику.
Для определения количества и качества тепловых ВЭР и ВЭР избыточного давления необходимо иметь соответствующую удобную форму баланса.
Удачным решением поставленной задачи является составление баланса в виде балансовой теплотехнологической схемы (БТТС), которая является статической расчётной характеристикой рассматриваемой системы. БТТС содержит информацию, дающую возможность оценить эффективность использования энергоресурсов во всех основных узлах технологического производства и наметить мероприятия по рационализации схемы.
3. Пример БТТС.

Показатели | Порядковые номера потоков | ||||||||||||||
---|---|---|---|---|---|---|---|---|---|---|---|---|---|---|---|
1 | 2 | 3 | 4 | 5 | 6 | 7 | 8 | 9 | 10 | 11 | 12 | 13 | 14 | 15 | |
Поток | HCl | HCl | пар | конденсат | этилен | этилен | пар | конденсат | сжатый воздух | сжатый воздух | пар | конденсат | конденсат | пар | реакционный газ |
Расход, т/ч | 11,6 | 11,6 | 0,56 | 0,56 | 4,3 | 4,3 | 0,56 | 0,56 | 19,6 | 19,6 | 1,2 | 1,2 | 20,0 | 20,0 | 36,0 |
Давление, МПа | 0,5 | 0,5 | 1,2 | 1,2 | 0,5 | 0,5 | 1,2 | 1,2 | 0,5 | 0,5 | 1,2 | 1,2 | 1,6 | 1,2 | 0,3 |
Температура, °С | 30 | 150 | 197 | 197 | 30 | 150 | 197 | 197 | 30 | 150 | 197 | 197 | 100 | 191 | 230 |
Индекс узла и тепловая мощность, кВт | Т-1 – 300 | Т-2 – 300 | Т-3 – 665 | Т-4 – 11700 |
Показатели | Порядковые номера потоков | |||||||||||
16 | 17 | 18 | 19 | 20 | 21 | 22 | 23 | 24 | 25 | 26 | 27 | |
Поток | реакционный газ | реакционный газ | воздух | воздух | реакционный газ | реакционный газ | вода | вода | реакционный газ | реакционный газ | рассол | рассол |
Расход, т/ч | 37,0 | 37,0 | 480 | 480 | 26,6 | 26,6 | 80,0 | 80,0 | 20,8 | 20,8 | 198 | 198 |
Давление, МПа | 0,3 | 0,3 | 0,0 | 0,0 | 0,3 | 0,3 | 0,3 | 0,25 | 0,3 | 0,3 | 0,3 | 0,25 |
Температура, °С | 105 | 60 | 25 | 50 | 60 | 40 | 25 | 35 | 40 | 10 | -15 | -12 |
Индекс узла и тепловая мощность, кВт | Т-4 – 3510 | Т-5 – 935 | Т-6 – 585 |
4. Анализ теплопотребления на основе БТТС.
Для анализа теплопотребления весьма эффективен так называемый метод "температурного соответствия". Как правило, исходные сырьевые и технологические потоки поступают в производство при температуре окружающей среды (от -30 до 25 °С) и подогреваются паром различных параметров до необходимых температур (чаще всего до 100÷150 °С). За редким исключением вполне обосновано использовать низкопотенциальные ВЭР для первой ступени подогрева этих потоков. При более широком рассмотрении и анализе энергоиспользования на химическом предприятии методом "температурного соответствия" выявляется возможность именно на основе утилизации низкопотенциальных ВЭР резко сократить потребление теплоты от внешних источников на цели отопления, вентиляции и ГВС (как правило, более чем на 50 %).
Следует отметить неадекватность поставленным задачам подхода, который делает упор на энергетический КПД агрегатов без учёта всей схемы. Например, энергетический КПД теплообменника 98 %, а используется он в схеме, где поток нагревается с 10 до 25 °С паром от ТЭЦ или котельной. Эксергетический температурный коэффициент продуктов сгорания в топке составляет 0,96, а нагреваемого конечного продукта только 0,08, что указывает на низкую эффективность оборудования. Причиной этого может являться изолированность выбора оборудования для каждой стадии и объединение в единую технологическую схему только на последнем этапе, что приводит к высокой экономичности отдельных узлов и оставляет без внимания огромные возможности рационализации энергопотребления при рассмотрении технологической схемы в целом.
Рассмотрение БТТС основных узлов процесса окислительного хлорирования этилена (пример БТТС) позволяет сделать следующие выводы:
- Для подогрева технологических потоков 1, 5 и 9 от 30 до 70 °С вместо пара можно использовать низкопотенциальную теплоту потока 16, который охлаждается воздухом от 105 до 60 °С. Расход пара на эту операцию сокращается на 30 %.
- Реакционный газ 24 охлаждается от 40 до 10 °С рассолом с температурой -15 °С, получаемым от парокомпрессионной холодильной установки. Тот же эффект охлаждения можно обеспечить, используя холод +5 °С, вырабатываемый на абсорбционной бромистолитиевой холодильной машине, в которой первичным теплоносителем является горячая вода, нагретая до 90 °С теплотой охлаждаемого потока 16. Расход электроэнергии сокращается при этом на 1,6 млн. кВт*ч/год.
Таким образом, БТТС позволяет:
- в наглядной и доступной форме представить полную картину потребления топлива, теплоты, холода, воды;
- получить представление о количестве и параметрах энергоресурсов, а также о расходе, температуре и прочих характеристиках потоков, с которыми теряется тепловая и механическая энергия;
- сопоставить параметры потоков по каждому узлу и сделать выводы о правильности выбора энергоносителей;
- оценить возможное изменение энергетических потенциалов всех потоков и влияние этого изменения на технологический процесс;
- определить возможности многоступенчатого использования теплоты и давления;
- выявить узлы, в которых могут использоваться ВЭР;
- наметить мероприятия по рационализации схемы и выполнить рационализированный теплотехнологический баланс.
Обеспечить высокую эффективность анализа энергопотребления любого производства можно только при системном подходе, начав работу с отдельных установок, отделений и стадий процессов, и переходя к цехам, производствам и предприятию в целом.